An extruder is a machine that is commonly used in the plastic recycling process to melt and reshape plastic materials. It works by heating plastic materials to a high temperature, causing them to soften and become pliable. The softened plastic is then forced through a small opening, or die, which shapes it into the desired shape.
In the context of plastic recycling, an extruder can be used to melt down used plastic products and materials, such as bottles and packaging, and shape them into new products. This process can help to reduce the amount of plastic waste that ends up in landfills and also reduce the need for new plastic to be produced, which can have environmental benefits.
Extruders can be used in a variety of applications, including the production of plastic sheeting, film, and pipes, as well as the manufacturing of a wide range of products, including automotive parts, home appliances, and packaging materials.
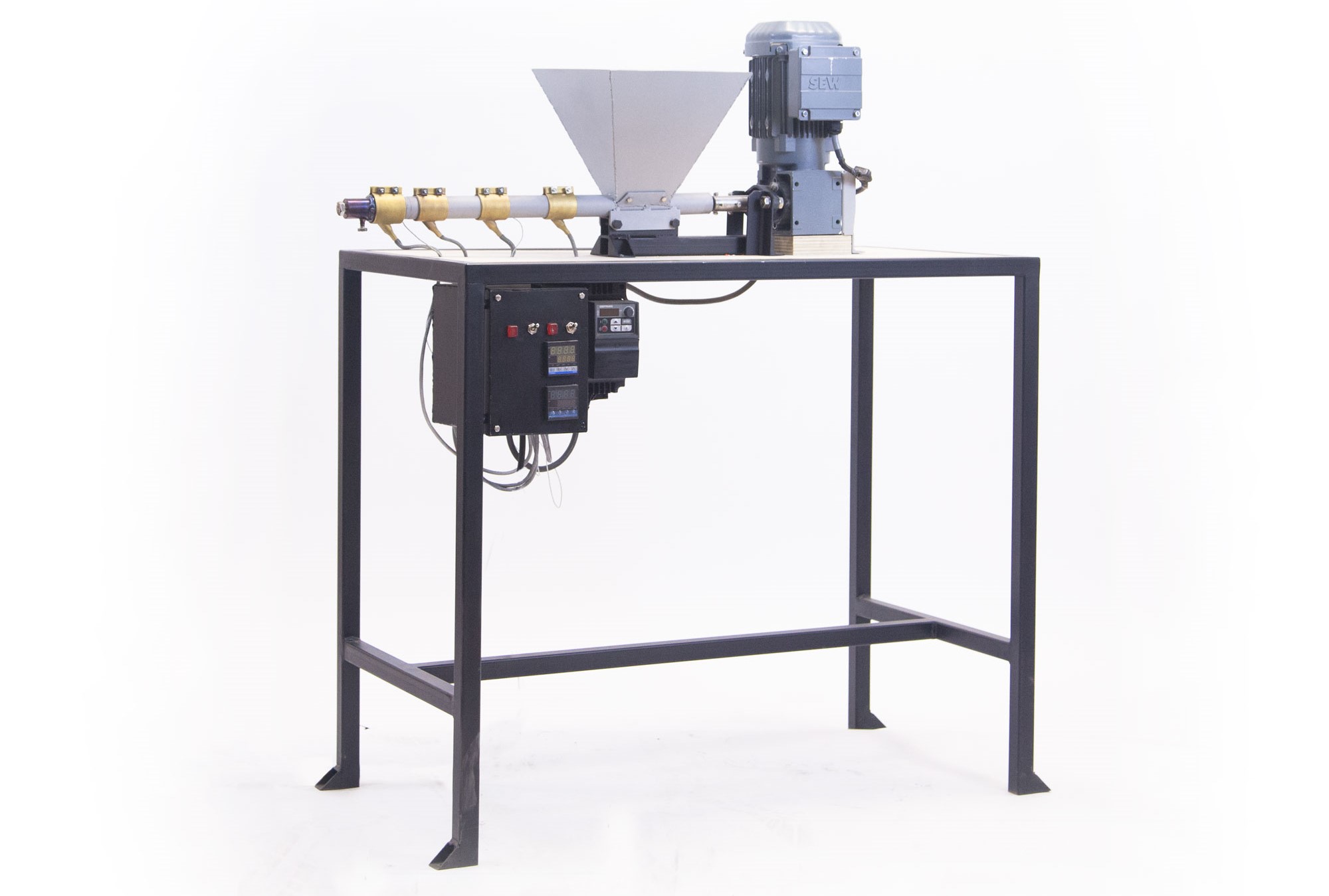
Extruders Specifications | Extruder V3 | Extruder V4 | Extruder Industrial |
Screw size | 25 x 500 mm | 30 x 700 mm | 65 x 1600 mm |
Output | 10-12 kg per hour | 18-20 kg per hour | 50 kg per hour |
Motor (ABB, Crompton) | 2 HP | 3 HP | 10 HP |
Gearbox Ratio | 20 :1 | 10:1 | 18: 1 |
Power Load | 4 Kw | 7 Kw | 20 Kw |
VFD (Speed Controller) | No | Yes | Yes |
Max Rpm | 70 Rpm | 100 Rpm | 80 Rpm |
Heating Zone | 2 Zones | 3 Zones | 3 Zones |
Power Supply | Single Phase | Three Phase | Three Phase |
Heater rating | 600 Watt | 1 Kw | 1.8 Kw |
Benefits of Extruders
- Plastic extrusion molding has a low cost and is more efficient.
- Reduces the change of inventory shortage and allows continuous manufacturing
- The extrusion molding is useful in creating complex shapes
- Plastic remains hot once they are removed from the extruder, therefore manufacturers can carry out post-extrusion changes to gain the desired product shape.